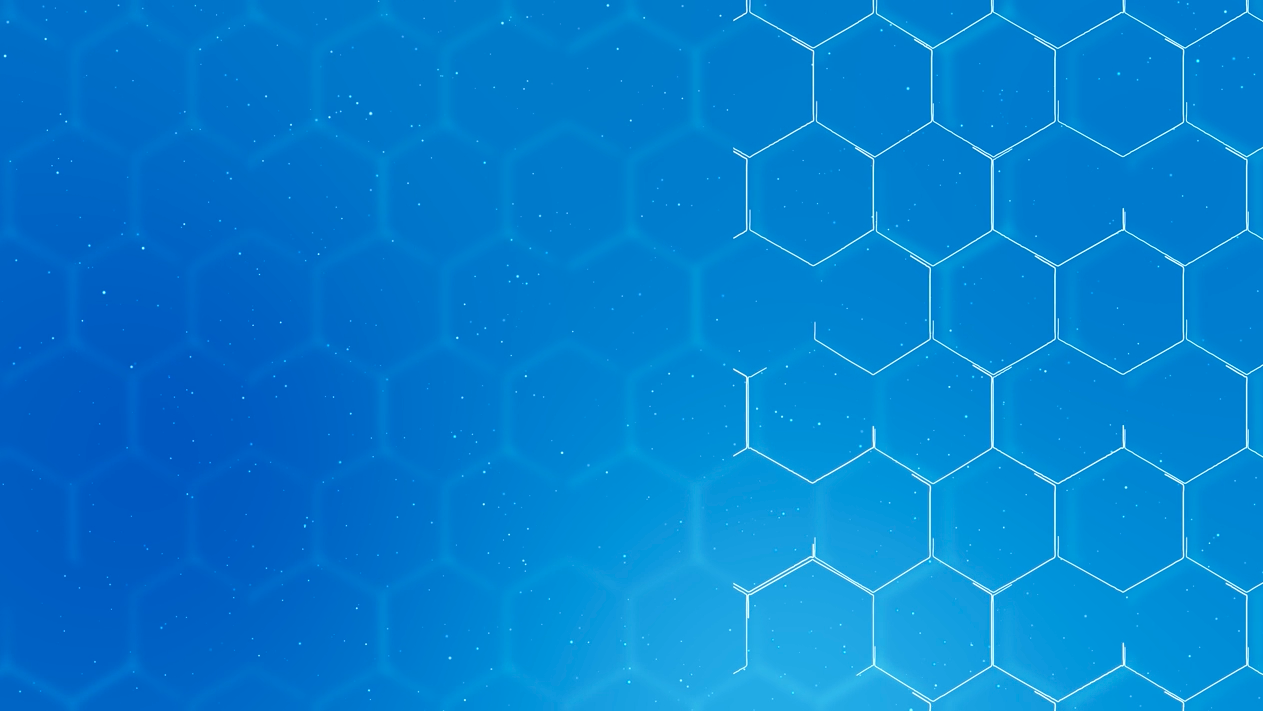
CASE STUDIES
We handle an extraordinary range of projects, each of which comes with its own challenges - largely anticipated, but still occasionally unforeseen. We are confident in our ability to achieve the result you are looking for.
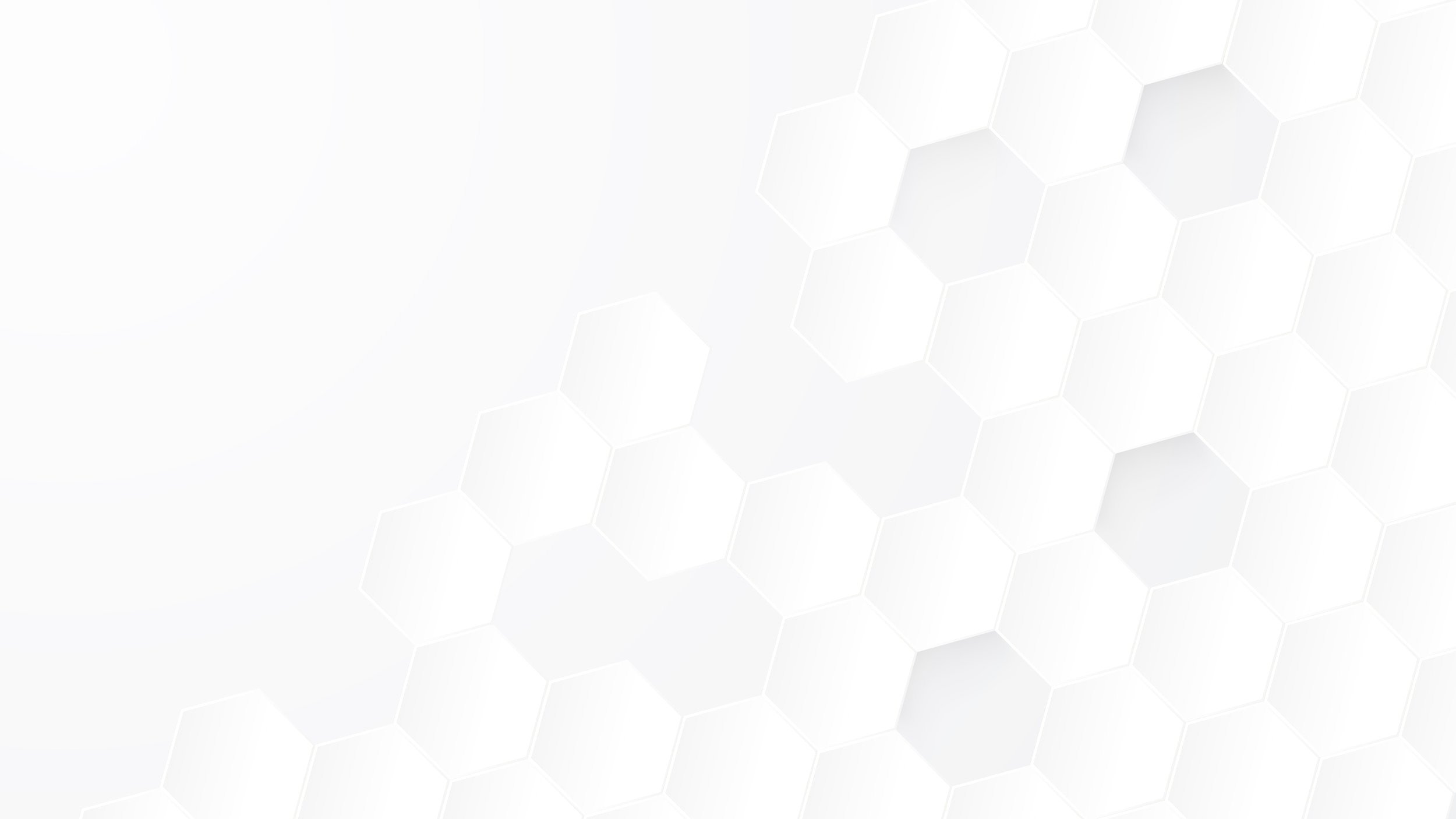
FLUTTER
LEAFLETS
WEST END PRODUCER
One of our regular clients reached out to us late on a Friday afternoon with an urgent request that was needed for a show opening the following Thursday…however it wasn’t a straightforward print job, so it would not only need to be turned around quickly, but we would need to find a way to make it work!
They needed artwork printed on the thinnest paper possible, and both sides, to be dropped into the audience from the theatre ceiling. It needed to be thin enough to ‘fly’, but thick enough to print on both sides.
With our years of experience, we immediately knew that their expectations of 35-55gsm weren’t realistic as this would be too thin to print on. We suggested 60gsm but didn’t know if this would be too thick for their ‘flying’ machine. So, one of our team headed to the theatre on Monday morning with samples to test that it worked in the theatre’s machines…hurrah it did! But would they still fly with ink on and how much ink was going to be too much?
After much back and forth with the artwork throughout Monday and Tuesday, we agreed on a design we thought had the best chance of working. Working through the night, we could hand deliver advanced copies to the producer to review on Wednesday. The job was delivered on Thursday morning, ready to be trialed with a live audience on opening night.
Here’s a summary of what we did:
Liaised with the client on what was needed for the job and what their expectations were.
Suggested 60gsm paper to achieve what they were looking for.
Made a visit to the theatre with sample paper to test it on their machines.
Once the test was a success we worked collaboratively with producers and designers on the artwork, giving advice on designs that stood the best chance of working.
Once the final artwork proof was approved it was another late night and early start so advance copies could be hand delivered to the producer to put their mind at rest.
The remaining print was delivered well in time for opening night.
The leaflets flew, and everyone was happy!
“No matter how last minute, or crazy, Hexagon are always able to deliver the impossible. Their industry knowledge is unparalleled and the team are kind, supportive & efficient - I could not do my job without their support, know how, and above and beyond high quality service...”
OTHER CASE STUDIES